Bridging Technology and Real-World Problems: Clarios’ Journey to Reduce Idle Time in Heavy-Duty Vehicles
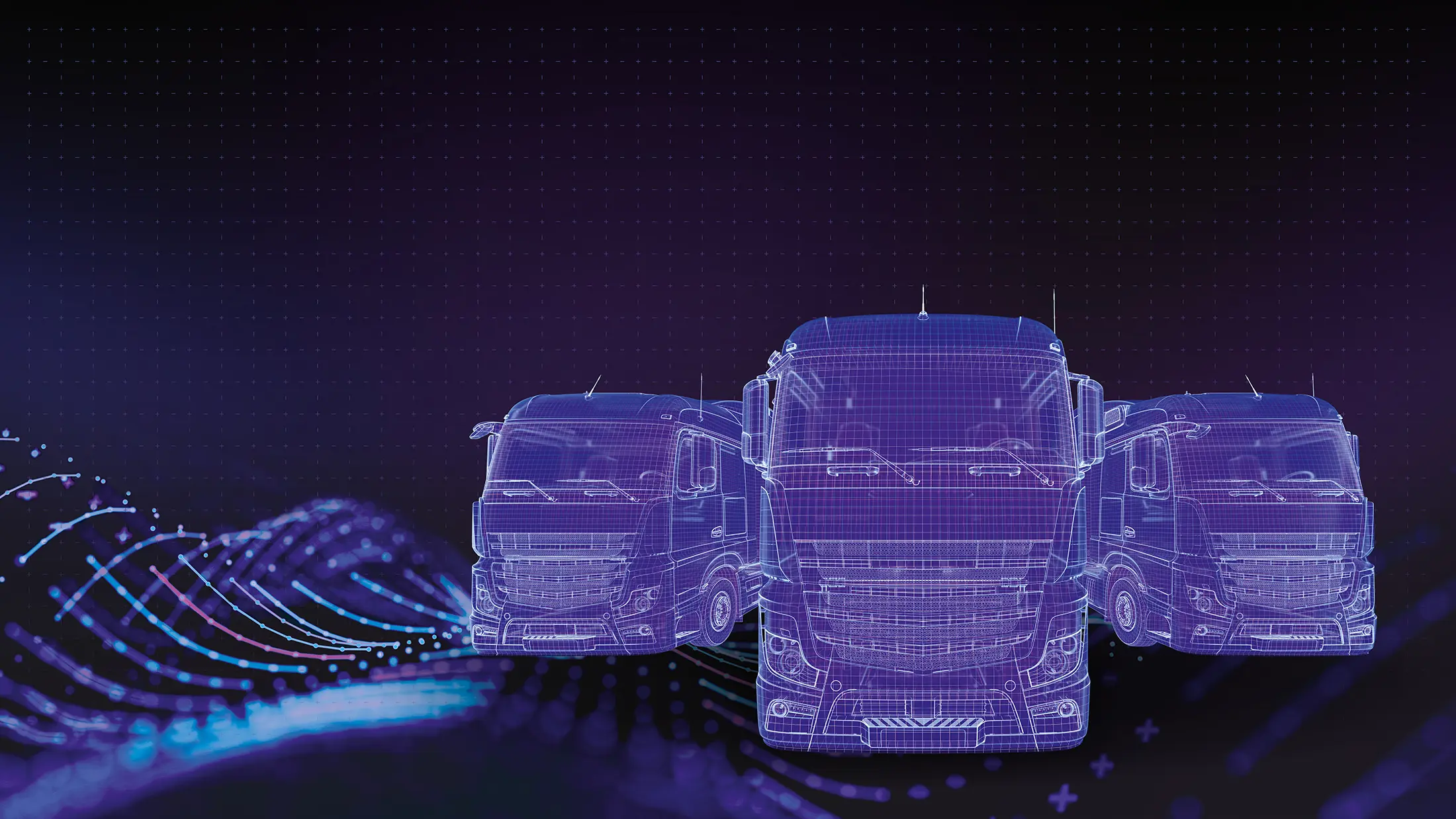
By Christina Yarnold, Director of Product Management, Clarios Connected Services
"Why don't we know when our car batteries need to be replaced?" my friend's mother-in-law asked me over coffee one weekend. She recounted a time when she was stranded with a dead battery, and it got me thinking. Despite all the advancements in vehicle technology, we're still grappling with fundamental issues like battery health and efficiency.
As an engineer who's spent most of my career in connected technologies, I love using tech to solve real-world problems. So when I joined Clarios and learned about our new Connected Services offering, specifically the idle reduction solution, I was thrilled. Here was an opportunity to address a tangible problem that affects not just individual drivers but entire fleets of heavy-duty vehicles.
We recently launched Clarios Connected Services, aiming to transform how drivers, commercial fleets, OEMs, and repair shops monitor battery power and health in real time. Combining artificial intelligence, machine learning, and cloud computing, we're bringing a new level of battery intelligence to the industry.
Our journey began with a pilot program with a fleet operator in Europe. We equipped several of their heavy-duty trucks with our idle reduction technology to see how it would perform in real-world conditions. The results were even better than we anticipated.
During the pilot, we observed a 40% reduction in unnecessary idling time. This translates to about €1,300 per vehicle per year in fuel savings and a reduction of 2,500 kg of CO2 emissions per vehicle annually. For a fleet operating numerous trucks, these numbers add up quickly, offering significant financial and environmental benefits.
But the pilot wasn't just about numbers; it was about learning and adapting. We worked closely with the fleet manager and the drivers, holding regular meetings to discuss the weekly results and gather feedback. One interesting discovery was that many of their vehicles were equipped with solar panels. These panels affected the battery charging patterns in ways we hadn't initially accounted for. Additionally, some trucks used hydraulic lifts powered by the battery, significantly impacting battery draw.
These insights were invaluable. They prompted us to refine our algorithms to account for these variables, making our solution more accurate and effective. It's one thing to develop a technology in the lab; it's another to see how it performs in the field and adapt accordingly.
Our approach embraces the lean startup mentality. We build quick prototypes, test them, gather feedback, and pivot as needed. It's a significant shift from the traditional manufacturing mindset, but it's crucial for innovation. We don't have all the answers upfront, and that's okay. What's important is that we're responsive and willing to adjust based on real-world data and customer input.
One of the most rewarding aspects of this project has been improving the driver experience. Heavy-duty vehicles with sleeper cabs are essentially homes on wheels for drivers. They need to manage their idle time to stay comfortable without violating regulations or wasting fuel. Our solution provides precise insights into battery status, allowing drivers to know exactly when they need to start or stop their engines. This not only saves fuel but also ensures they won't end up stranded with a dead battery.
I remember one driver telling us how much he appreciated the clear notifications on his in-cab tablet. Instead of relying on intuition or past experience, he now had accurate information at his fingertips. It's moments like these that remind me why I love what I do.
Looking ahead, we're excited to see that this fleet operator is expanding our idle reduction solution to additional vehicles within their fleet. It's a significant milestone that validates the hard work our team has put in and demonstrates the market demand for such innovations.
We're not stopping here. We're planning to incorporate predictive health alerts into our solution, which will proactively inform customers of potential battery issues before they lead to unexpected downtime. Imagine a system that can tell you weeks in advance that your battery needs attention. It's about being proactive rather than reactive, saving time, money, and headaches.
We're also considering ways to engage more with our colleagues across Clarios. Great ideas can come from anywhere, and we're working on launching internal initiatives to gather new ideas and perspectives. Innovation is a team sport, and the more minds we have working on these challenges, the better our solutions will be.
Reflecting on that conversation over coffee, I'm reminded of the importance of staying connected to real-world problems. Technology isn't just about what's possible; it's about what's practical and beneficial for people. At Clarios, we're committed to using our expertise to make a positive impact, one battery at a time.